'Flow' chest of drawers
- Jonathan Pearce
- Dec 20, 2019
- 3 min read
Furniture. Yes, in addition to making jewellery boxes, I do also make furniture .
This commission was for a chest of drawers, that would be used as a filing cabinet. The chest was to be sited in the living room, in place of an upright piano.
Simple, practical, clean lines was the basic requirement specification. A few visits to meet the client, with veneer and wood samples led to the design - 'Flow' chest of drawers.
I had finished the 'Flow II' jewellery boxes, and I took one along just to show some of my work. I had been playing with the idea of carving a similar pattern on the drawer fronts, but it is hard to explain. Having a physical box there allowed the idea to be seen. And the box and shaping is so tactile.
The box sold it. Agreed. An oak chest of drawers, with fronts that have the flow pattern.

So the carcass, drawer fronts, and part of the drawer boxes (front and back) are oak, and the drawer box side are maple.
A lot of timber, and I mean a lot! This is just some of the timber, the carcass, the legs, the drawer frames (the hidden dividers that hold the sides of the carcass together and that tradition drawers run on).
Not included in all this is the timber for the drawers themselves!
Note how the wood comes in rough planks. Means hours at the machines getting it ready for use!

Here the carcass is being glued up.
The drawer frames can be seen - the sort of ladder structure. Having the frames made like a ladder means the overall weight of the carcass is reduced.
It is a big glue-up. The carcass is 1.2m wide. The picture looks a bit strange as the carcass is actually on its side - just makes glue-up easier.
Two more loads of timber. The oak and maple for the drawer boxes. All cut over size and thickness, and then left for a few weeks (while I was on holiday) to dry and stabilize.
Drawer boxes need stable timber so they don't twist and warp. So don't rush the drying process.
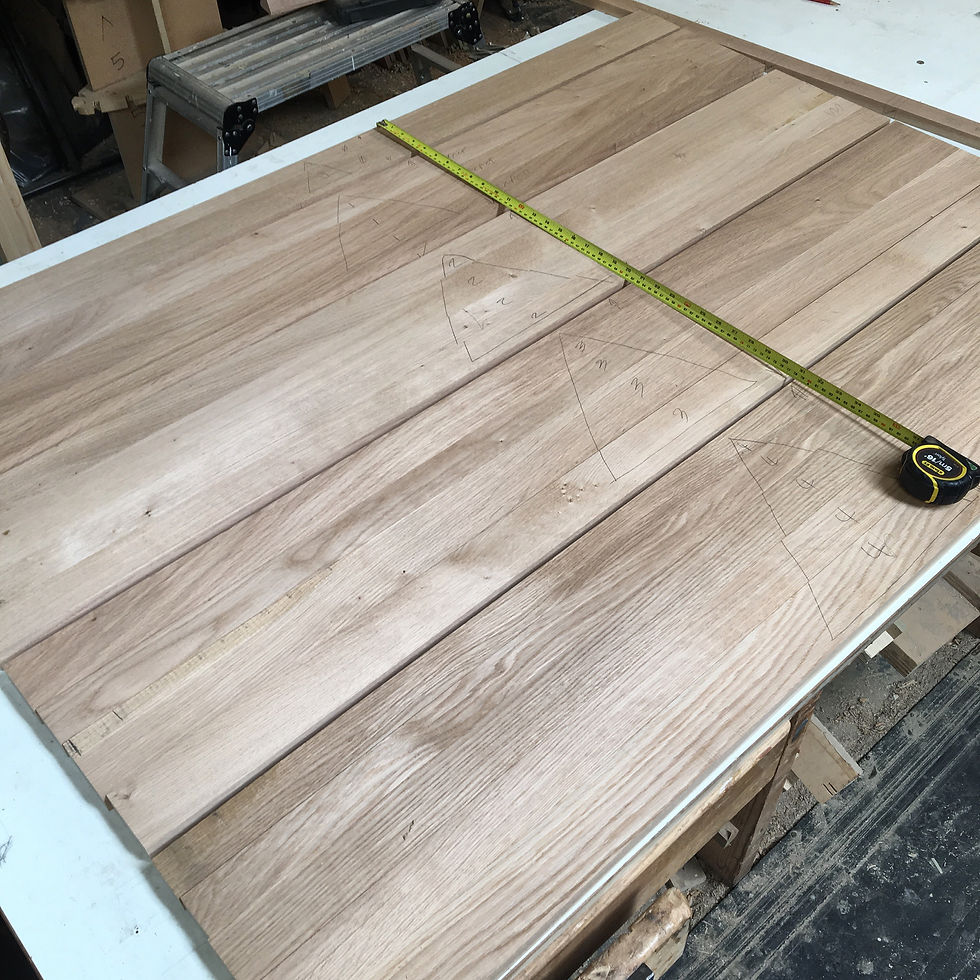
This is the timber that will be used to make the drawer fronts.
Each front is made up of a number of strips of wood. The position of each strip is considered, as a good even grain pattern is wanted in the final piece.
Another reason this mix-and-match process of arranging the strips of wood is required, is that the timber comes from a number (five in this case) planks of wood, and mixing the position helps even out the variance of colour and grain.
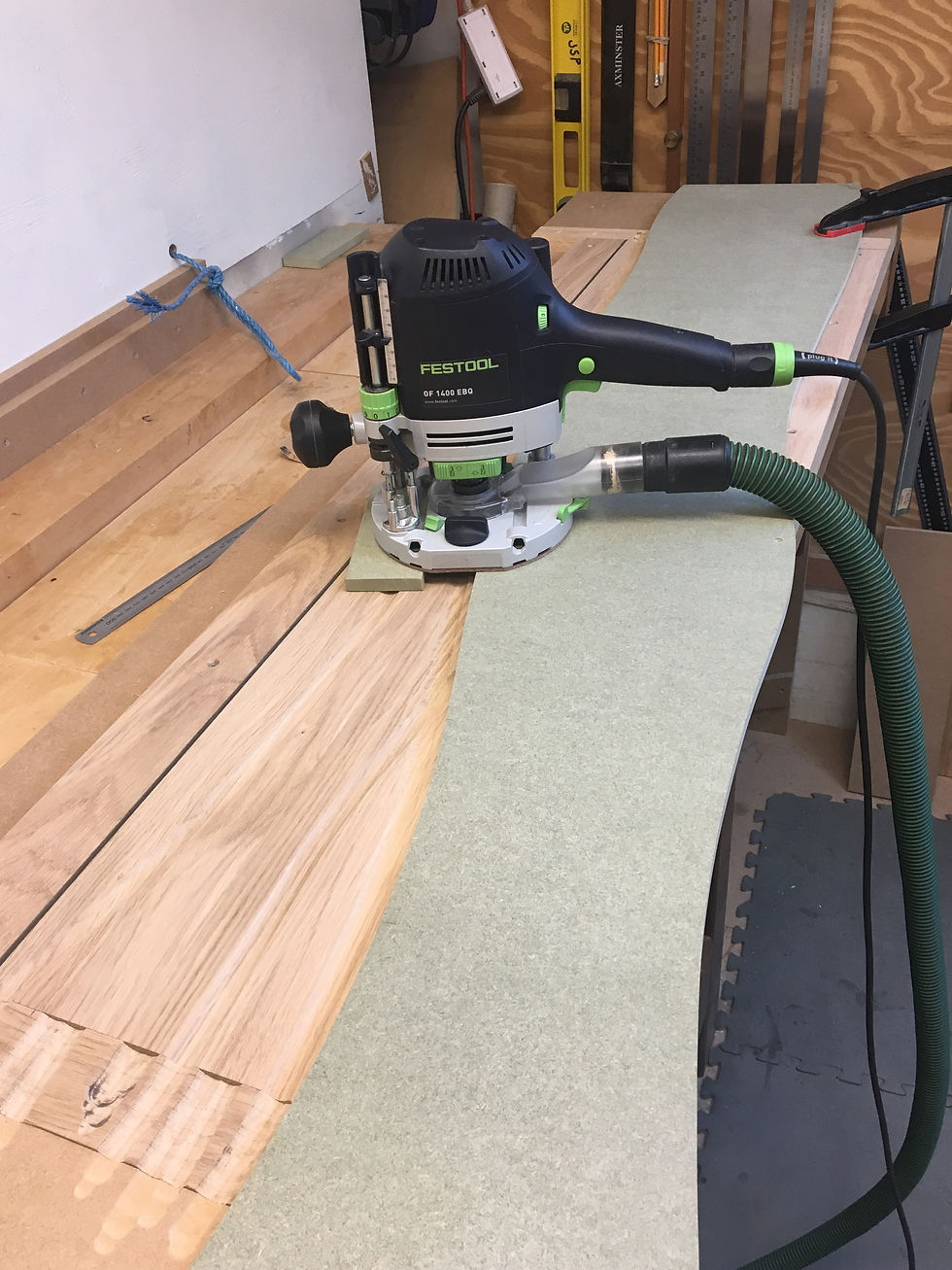
Next comes the fun bit.
After all the drawer fronts are glued up, I then have to route the flow pattern across them.
Various templates are used that are curved, and by moving them a pattern is slowly built up.
It is all random, all depends where I place the template and how deep each cut is made.
Each totally unique.

A few cuts made into the drawer front, the pattern starts to emerge.
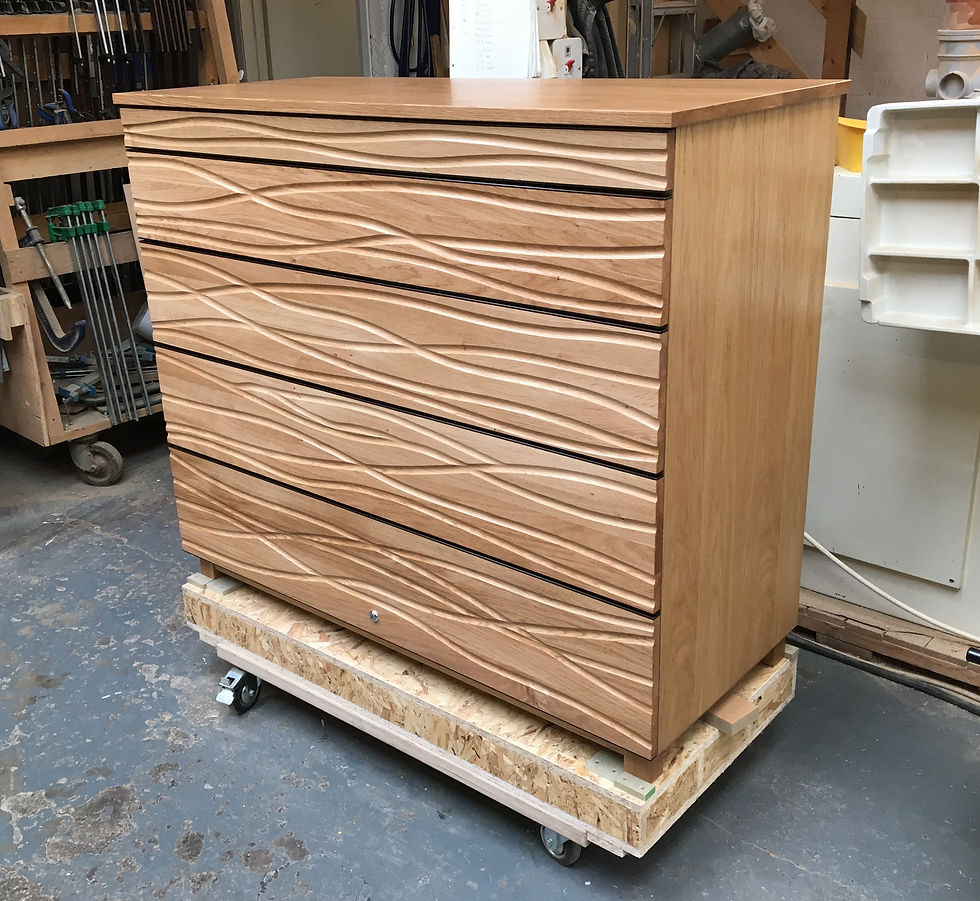
Here is the finished piece, still in the workshop. The pattern on the fronts can be seen, and they give a very tactile feel to the drawer fronts.
Each front is edged with fumed oak, that add a pleasing eye detail to each drawer front.
The top most drawer is tiny - it is a pull out flap that is used to place items on when removed from the drawers.

Looking along the fronts of the drawers, the fumed oak edge detail can be seen.
Each flow pattern crosses a number of others, and where they do is a really interesting detail to feel. The individual cut can be felt, with the depth of each adding to the texture.
The piece is finished using hardwax oil.
Here is the finished piece, delivered to its new home.

Comments